Every product goes through the initial prototype stage. Before you can bring a product to market and produce it at any scale, you have to hold it in your hands. Does it function as designed and can you manufacture the parts required? These are the major questions.
You also have to transform your designs into a physical model or several to be assembled. For that, you want to find the optimal parts suppliers equipped with matching manufacturing processes, mostly likely 3D printing.
It's also important to begin thinking about what happens when you scale up from 3D printing to CNC machining or injection molding. The goal is to reduce time and cost, so you can move from a look-and-feel object to a customer-ready product without altering designs drastically to fit each new manufacturing stage.
This article explores the best manufacturing processes and technologies for initial or early-stage prototyping.
Curious about the price of initial prototyping?
Check out our 3D printing services Upload your CAD file for a free, instant quote
What is an initial prototype?
An initial prototype is a model produced at the earliest stages of product development that lets you test your product’s look and feel (and base functionality, depending on the product). Prototypes can be as simple as 3D-printed objects representative of your final product or somewhat more complex models for testing performance and mitigating risk.
Another way to think about prototyping is that it's the first tangible attempt to solve the problem your product hopes to solve.
Prototyping is also about spotting design and manufacturing risks early in the innovation cycle. For instance, if you know that your product will be used in the aviation or automotive spaces, you want to get an indication of strength, flexibility and durability sooner rather than later. Medical products go through many rounds of compliance testing, so carrying out pre-compliance work in the prototyping phase will save you a lot of time, money and anxiety in the future.
At its core, initial prototyping answers the fundamental question: does my design function in the physical world? This is a question you need to answer rapidly.
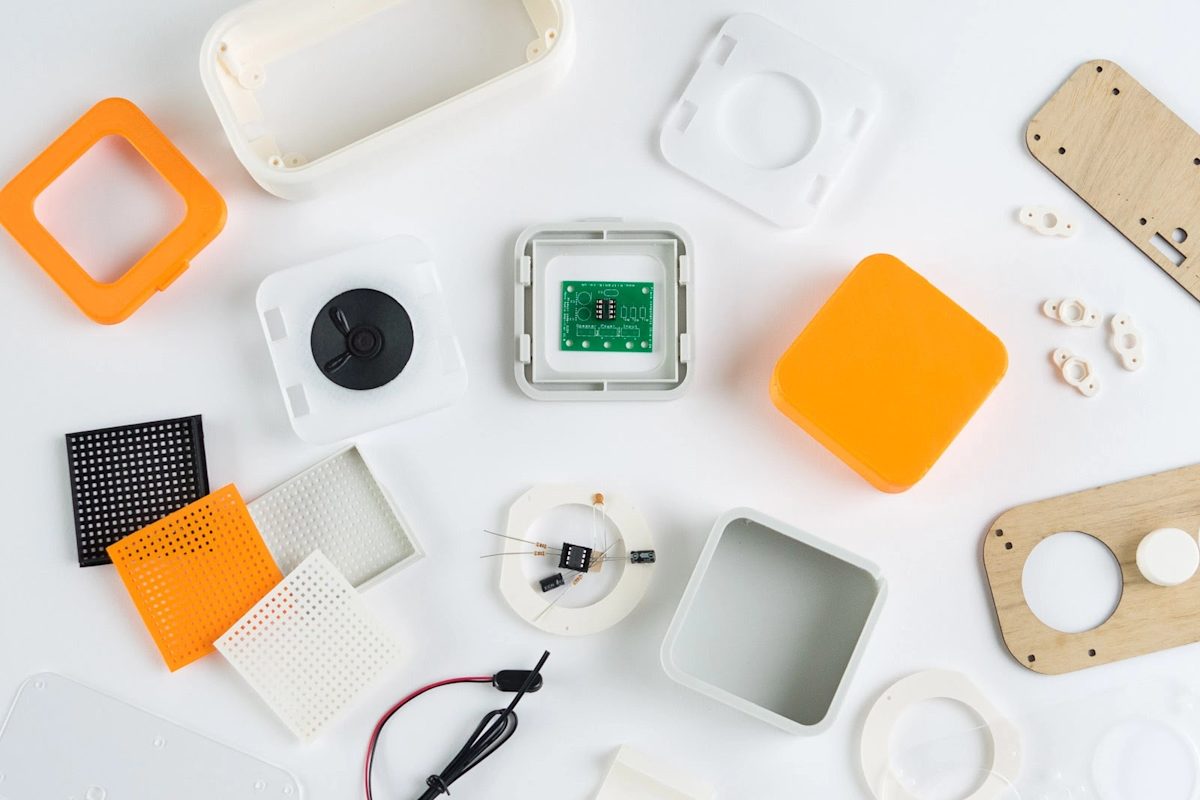
What is rapid prototyping? Your first product prototypes, but faster
Rapid prototyping is the practice of quickly fabricating physical parts, models or assemblies. Using CAD (computer-aided design) and faster-turn manufacturing methods like 3D printing to churn out several more physical iterations, designers and engineers can use the rapid prototyping approach to develop products faster.
In product development, this method spans the initial and functional phases of prototyping. Rapid prototyping and additive manufacturing are generally lumped together, though this depends on the type of product you’re producing. Whether you’re trying to create parts for initial or functional prototyping, you can use certain 3D printing, as well as CNC machining and sheet metal fabrication in some cases.
What are the optimal manufacturing processes for initial prototyping?
Dreaming up a design for a product is one thing. Getting it made is something else entirely. In this section, we cover how to transform a napkin drawing (or a fully-fledged CAD file and technical drawing, to be fair) into a physical object.
The most cost-efficient technologies for manufacturing your initial prototypes are prototyping FDM, prototyping SLA (both 3D printing processes) and sheet metal fabrication.
Highlighting cost, prototyping FDM is the cheapest way to produce proof of concept components. FDM is ideal in most cases if you want to see a basic physical manifestation of your product in the real world. However, it’s not ideal if you care about surface finishes or need moving parts.
Prototyping SLA is a bit more geometrically flexible than FDM and it comes at a similar price point for smaller batches of prototypes. SLA is good at producing organic shapes, and designs that work well with SLA tend to scale to injection molding.
Both of these 3D printing technologies work really well for producing plastic models that not only give you a clearer picture of what the product may look like several iterations from now, but also provide your sales teams something to show early clients. How you use the initial prototype is up to you, but it’s good to remember that you can take the first prints out of the R&D labs and put them into clients’ hands.
Choosing between FDM and SLA comes down to what kinds of geometries you’re going for, as both will net a cost-effective price tag. Definitely avoid metal 3D printing (DMLS), as it’s only really good at making parts that can’t be made any other way. So you’ll struggle when it comes time to start machining or molding designs previously produced by DMLS.
Producing initial prototypes with sheet metal is a whole different story. With sheet metal, the technology doesn’t change drastically from prototyping to much higher volumes of production. The machines begin to get more complex the closer your design gets to getting into the hands of end-users and customers, but it’s not like going from FDM to SLS (selective laser sintering) or MJF (multi jet fusion), which are worlds apart.
One way to ensure that initial prototyping costs aren’t astronomical is to avoid setting up automated pressing and bending. There’s not much of a reason to do this before the production phase.
How do you reduce cost and lead time for prototyping?
With additive technologies like SLA and especially FDM, manufacturing the initial prototypes is cost-effective. FDM and SLA materials aren’t that pricey, and the machines don’t require the same operational skill and attention as SLS, MJF and production-grade CNC systems and injection molding setups.
One thing to watch out for is the cost of shipping. Depending on where you’re sourcing parts from, the shipping costs may be what makes initial prototyping suddenly quite costly. Our recommendation for this is to print several components at once. You’re looking to iterate fast and fail faster, so printing tens of parts will be cheaper than printing a single component, waiting, and then getting another sole print shipped.
You can also save money and print time by using the standard densities of FDM and SLA. There’s often no need to add more material if the goal is to get a first glimpse of the product. If you don’t have the right density to use for your part, always defer to the Protolabs Network's manufacturing partner (MP), though a good rule of thumb is to always use the lowest density you can.
No matter which technology you choose to use for your initial prototyping, the best practice is always to make your design as future-proof as possible. Remember that you’re not designing your part for FDM or SLA or even more advanced 3D printers. You’re designing the components of your product to be produced at scale (most likely with injection molding).
Understanding the basic principles of FDM and SLA will really help you save time and money in the short term, but don’t make design concessions that will be hard to undo when it comes time to produce parts with CNC machining and injection molding. Design for a successful print now, but not at the cost of future production.
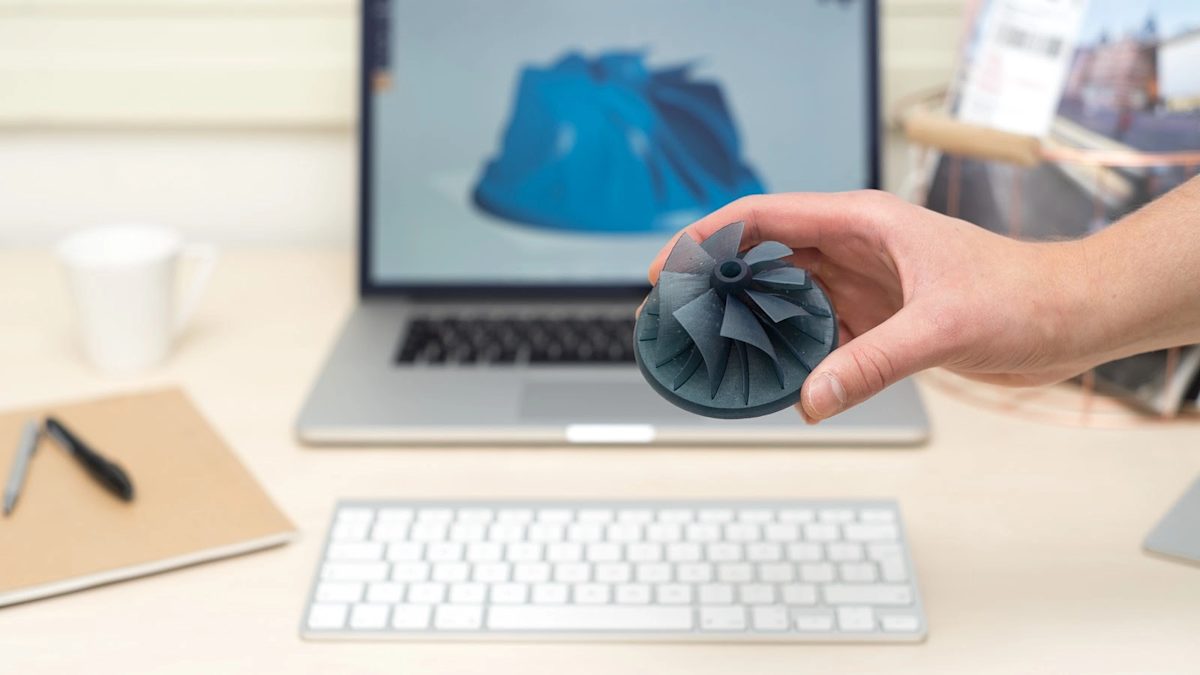
How do you move from initial prototyping to functional prototyping?
At the initial prototyping stage, you’re putting components together to solve basic design problems. You don’t need to present anything to investors or the public just yet; mostly, you need to know whether product features work as intended. If you press a button on the product, will it do as it’s designed?
This means that your manufacturing needs are minimal. High tolerances aren’t required and technical drawings may not even carry a manager’s signature. Initial prototyping is about getting cost-effective parts quickly so you can fail fast. Think of it as manufacturing to render your napkin sketch in physical space.
Functional prototyping is more demanding when it comes to part sourcing. A functional prototype should prove whether the design solves the issue your product is intended for, and give you a good indication of the future return on investment of the design. What you assemble has to function almost as well as the final product should.
So for functional prototyping, you still want to get parts made fast and mostly from the same materials, but using higher caliber processes and technologies. SLS and MJF become more viable at this stage, as does CNC machining—unless your final product is polymer-based, this is when you start using metal components.
For functional prototyping, we recommend using Protolabs Network's fast, local offering, leveraging CNC machine shops within your custom clearance zone. Parts may be a little more expensive than those sourced overseas, but you need far fewer of them at this stage and the time saved will quickly balance out any extra euros spent on local speed.
Product prototyping is possible in-house - what’s the benefit of using a manufacturing network?
The truth is that anyone can purchase a cheap FDM printer and start printing prototype components. Consumer-grade FDM printers can cost as little as €200 or €300, so a lot of companies buy a few of them and plunk them in their R&D offices.
The issue with this solution is that it doesn’t take into account the amount of time you need to master an FDM machine. Getting the most out of a freshly unboxed 3D printer will take a lot of tinkering.
Since the beginning, Protolabs Network has worked with passionate, detail-oriented 3D printing enthusiasts, many of whom have become vetted suppliers. All the smaller-scale 3D printing suppliers outfitted for initial prototyping have learned their machines to the point of mastery and can produce parts that will always come out more robust and of higher quality than a home or in-office print. And many of them have scaled from enthusiasts to industrial suppliers capable of producing components far beyond initial prototypes.
The benefit of having these passionate makers onboard is that we can help fill a production gap at the initial prototyping stage that would normally be filled with far more hours figuring out how to get a decent printout of a machine fresh out of the box. Admittedly, the simpler printers have a low barrier to entry, but it’s still likely a waste of time to have highly skilled engineers toiling away with an Ultimaker manual instead of focusing on the design work that matters.
And even if you do have machines at the ready, why tie them up when Protolabs Network has far more capacity to spare? Entrusting distributed manufacturing can free up so much time and resources to help you focus on the design work that matters.
Are you interested to learn more about how Protolabs Network can help you make initial prototypes? Explore our online 3D printing services or upload a CAD file to the quote builder for a free, instant quote. For more information, reach out to networksales@protolabs.com.
Are you ready to start sourcing custom parts for initial prototyping?
3D print parts with FDM 3D print parts with SLA Make metal parts with sheet metal fabrication service Go to the quote builder